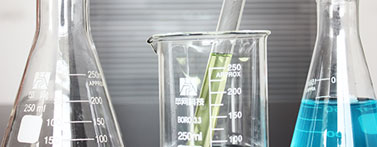
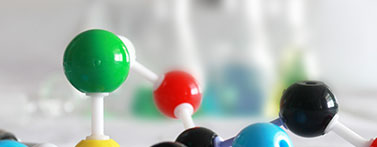
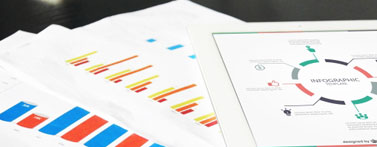
1. High selectivity: Selectivity of the carbonylation catalyst is above 99%, and the selectivity of hydrogenation catalyst is above 98.5%.
2. High efficiency of hydrogenation catalyst: Efficiency of HighChem catalyst is two to five times of competitor’s equivalent product. Our catalyst does not pulverize easily during reaction process, and does not cause a drastic drop in reactor pressure in any short durations.
3. Long catalyst life: The carbonylation catalyst of HighChem has been used in the Xinjiang Tianye Phase I SEG transfer project for over 3 years, with expected catalyst life of more than five years. The hydrogenation catalyst of HighChem is the only catalyst that has more than one year’s operating performance in the market with a service life of about one and one-half years.
4. Small loading quantity: With a low bulk density, lesser loading quantity is required in the same reactor.
5. High expertise in catalyst production: High level of quality assurance and flexibility in production schedule to meet customer requirements.
1.Safety: We holds more than 30 years of expertise in handling of highly explosive intermediate products (nitrite methyl) and operation of DMO unit.
2. Stability: The 50,000-ton/yr Xinjiang Tianye Phase I project achieved output of 44,000 tons in the startup year and output of 5.2–5.4 million ton/yr for the last three years.
3. Low unit consumption: Based on proven track records, HighChem process unit consumptions achieves the lowest level compare to competitors in the industry.
4. Technology optimization: Together with UBE Industries, we optimize existing technologies and are committed to the research and development of process scale up tailored to customer needs.
5. Stable and reliable product quality: We received positive feedback from downstream polyester manufacturers (Zhejiang Tongkun and Shuangtu), ethylene glycol produced from CTEG technology offers the most stable and reliable quality in the industry.
6. Overall performance: As of July 2017, we have completed CTEG transfer package at 14 locations with a total capacity reaching 4 million ton/ yr.
SEG offers customers with a combination of cost advantage in raw material and technological advantage.
SEG® produces the EG of the highest quality at lowest overall cost in industry worldwide.